The Scientific Research Behind Porosity: A Comprehensive Overview for Welders and Fabricators
Comprehending the detailed systems behind porosity in welding is crucial for welders and makers making every effort for remarkable craftsmanship. As metalworkers dive right into the depths of this sensation, they reveal a globe regulated by various variables that influence the formation of these tiny spaces within welds. From the structure of the base materials to the intricacies of the welding process itself, a wide range of variables conspire to either exacerbate or relieve the presence of porosity. In this comprehensive overview, we will unravel the science behind porosity, exploring its impacts on weld high quality and unveiling advanced strategies for its control. Join us on this trip with the microcosm of welding blemishes, where precision satisfies understanding in the quest of remarkable welds.
Understanding Porosity in Welding
FIRST SENTENCE:
Evaluation of porosity in welding exposes critical understandings right into the integrity and top quality of the weld joint. Porosity, defined by the visibility of cavities or voids within the weld metal, is a typical issue in welding procedures. These voids, if not effectively dealt with, can compromise the structural stability and mechanical properties of the weld, resulting in possible failings in the completed product.

To spot and measure porosity, non-destructive screening approaches such as ultrasonic screening or X-ray examination are often employed. These techniques allow for the identification of internal defects without compromising the integrity of the weld. By examining the dimension, form, and circulation of porosity within a weld, welders can make educated decisions to enhance their welding processes and accomplish sounder weld joints.

Variables Affecting Porosity Development
The event of porosity in welding is affected by a myriad of factors, ranging from gas shielding effectiveness to the intricacies of welding parameter settings. One essential element contributing to porosity development is insufficient gas securing. When the shielding gas, usually argon or CO2, is not efficiently covering the weld pool, atmospheric gases like oxygen and nitrogen can contaminate the liquified steel, resulting in porosity. In addition, the cleanliness of the base products plays a significant role. Contaminants such as corrosion, oil, or dampness can evaporate throughout welding, developing gas pockets within the weld. Welding specifications, including voltage, existing, travel speed, and electrode kind, additionally effect porosity development. Utilizing improper setups can produce excessive spatter or warmth input, which subsequently can lead to porosity. The welding technique used, such as gas read the article metal arc welding (GMAW) or shielded steel arc welding (SMAW), can influence porosity development due to variants in warm distribution and gas protection. Understanding and regulating these aspects are necessary for minimizing porosity in welding procedures.
Results of Porosity on Weld Quality
Porosity development significantly jeopardizes the architectural integrity and mechanical properties of welded joints. When porosity is existing in a weld, it develops voids or tooth cavities within the product, reducing the general toughness of the joint. These voids serve as anxiety focus points, making the weld much more prone to cracking and failure under tons. The existence of porosity additionally weakens the weld's resistance to corrosion, as the caught air or gases within deep spaces can react with the surrounding environment, resulting in deterioration with time. In addition, porosity can hinder the weld's ability to endure pressure or effect, additional endangering the total top quality and integrity of the bonded framework. In critical applications such as aerospace, automotive, or structural constructions, where safety and sturdiness official statement are vital, the damaging impacts of porosity on weld high quality can have serious repercussions, stressing the value of lessening porosity with appropriate welding methods and procedures.
Techniques to Minimize Porosity
To boost the quality of welded joints and guarantee architectural integrity, welders and fabricators use details strategies targeted at reducing the development of voids and tooth cavities within the material throughout the welding process. One reliable method to decrease porosity is to guarantee correct material prep work. This includes detailed cleaning of the base steel to remove any type of impurities such as oil, grease, or dampness that could contribute to porosity development. Additionally, utilizing the ideal welding parameters, such as the right voltage, current, and travel rate, is important in preventing porosity. Preserving a regular arc size and angle during welding likewise assists lower the you could check here possibility of porosity.

Making use of the appropriate welding method, such as back-stepping or utilizing a weaving activity, can likewise assist disperse warmth equally and minimize the chances of porosity formation. By applying these strategies, welders can effectively lessen porosity and create top quality bonded joints.
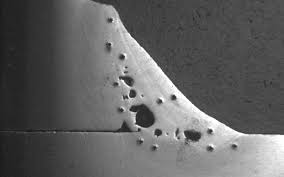
Advanced Solutions for Porosity Control
Applying advanced modern technologies and ingenious methods plays an essential role in achieving exceptional control over porosity in welding procedures. Additionally, utilizing sophisticated welding methods such as pulsed MIG welding or modified environment welding can also assist reduce porosity concerns.
An additional innovative remedy entails using innovative welding equipment. As an example, utilizing equipment with integrated functions like waveform control and advanced source of power can enhance weld high quality and decrease porosity threats. The application of automated welding systems with exact control over criteria can dramatically decrease porosity issues.
Furthermore, incorporating advanced monitoring and inspection technologies such as real-time X-ray imaging or automated ultrasonic testing can aid in spotting porosity early in the welding process, allowing for immediate corrective activities. On the whole, incorporating these sophisticated services can significantly boost porosity control and boost the general high quality of bonded elements.
Final Thought
Finally, recognizing the science behind porosity in welding is important for welders and makers to generate top quality welds. By identifying the elements affecting porosity formation and carrying out methods to lessen it, welders can boost the overall weld top quality. Advanced remedies for porosity control can additionally improve the welding process and make certain a strong and dependable weld. It is very important for welders to continually inform themselves on porosity and implement ideal methods to achieve optimum results.